The writer is a shareholder of Goodpack.
David Lam, executive chairman of Goodpack.
NextInsight file photoRUBBER USED TO be transported in wooden crates only. Twenty five years ago, Singaporean David Lam hit upon the idea of developing alternative packaging for rubber after witnessing how difficult it was to remove wood splinters from rubber after crates fell from a lorry in Thailand. (See: GOODPACK: The Man Behind Its Sterling Results)
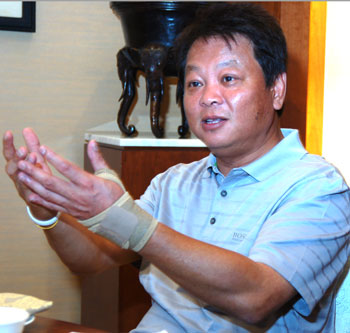
NextInsight file photoRUBBER USED TO be transported in wooden crates only. Twenty five years ago, Singaporean David Lam hit upon the idea of developing alternative packaging for rubber after witnessing how difficult it was to remove wood splinters from rubber after crates fell from a lorry in Thailand. (See: GOODPACK: The Man Behind Its Sterling Results)
Mr Lam developed what came to be known as intermediate bulk containers (IBCs), and founded Goodpack.
Made of steel, the IBCs have several advantages. They can be reused for many years, saving more trees from being felled to make wood crates.
They obviate costly disposal of discarded wood crates.
Lastly, empty IBCs can be collapsed into a single slab, saving transportation cost.
Made of steel, the IBCs have several advantages. They can be reused for many years, saving more trees from being felled to make wood crates.
They obviate costly disposal of discarded wood crates.
Lastly, empty IBCs can be collapsed into a single slab, saving transportation cost.
Goodpack has patented its IBC. It has grown its IBC fleet to 3 million. Its world-wide network serves 68 countries. All these are formidable entry barriers to its business.
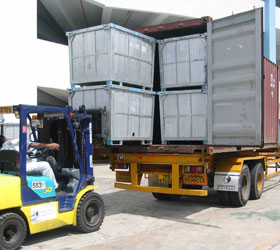
Goodpack has been exploring new applications for IBCs.
Fruit juice, mostly transported in drums, was first identified.
According to Goodpack's IPO prospectus, a TEU's (twenty-foot equivalent unit) payload with 80 drums weighs 16 tonnes only.
On the other hand, a TEU with 16 compactly-packed IBCs (fitted with bladders to hold liquid) can have a payload of 22.4 tonnes.
On the other hand, a TEU with 16 compactly-packed IBCs (fitted with bladders to hold liquid) can have a payload of 22.4 tonnes.
While the fruit juice market is large and the prospect of IBCs being adopted is good, Goodpack has refrained from putting more resources in this sector because of low utilisation of IBCs outside harvest seasons.
Earnings catalysts from autoparts business
For a few years, Goodpack has been in earnest talks with car manufacturers on transporting automotive parts in IBC.
For a few years, Goodpack has been in earnest talks with car manufacturers on transporting automotive parts in IBC.
The pace of progress probably reflects the need to assure major car manufacturers that Goodpack has a reliable system to track IBCs carrying automotive parts to ensure their timely arrivals for assembly.
Lending weight to this proposition is an RFID Journal article on the massive exercise by Goodpack to tag all its IBCs with RFID devices.
Lending weight to this proposition is an RFID Journal article on the massive exercise by Goodpack to tag all its IBCs with RFID devices.
It is not known when exactly the US$8 million tagging exercise (estimated to take two years from 2011) will be completed. Will car manufacturers place their orders for IBCs after all IBCs have been tagged, or does Goodpack have to do more to win orders?
According to DBS Research, Goodpack has made some progress in this business segment, clinching 10 new customers in FY13, bringing the total to 16. Moreover, evaluation by a major OEM in Europe has now reached an advanced stage.
Goodpack has borrowed heavily some US$300m, but the bulk of it - some US$230m - is sitting as idle cash. No explanation has been offered for this costly arrangement (resulting in US$12m interest payment a year) that dents the profit.
Could the idle cash be on standby for the purchase of new IBCs at short notice for use by car manufacturers?
Goodpack's net profit, dented by high interest cost, may not be as good a measure of performance as Earnings before interest and tax (Ebit), which does not factor in interest cost.
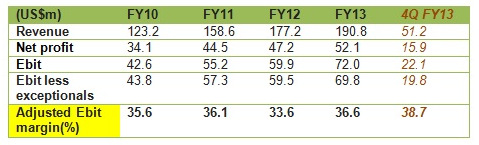
The high adjusted Ebit margin in 4Q FY13 of 38.7% was probably due to business arising from the ramping up of two synthetic rubber factories on Jurong Island.
Given that there is little seasonality in its business, is Goodpack set for much stronger profit growth in the current FY?
In the meantime, Goodpack shareholders are looking forward to the proposed final dividend of 2 cents and special dividend of 3 cents.
Click on the above image for a video on how Goodpack's IBCs work.
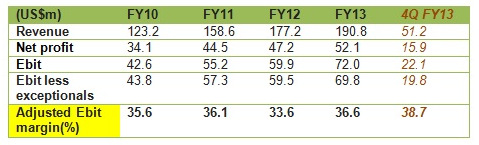
The high adjusted Ebit margin in 4Q FY13 of 38.7% was probably due to business arising from the ramping up of two synthetic rubber factories on Jurong Island.
In the meantime, Goodpack shareholders are looking forward to the proposed final dividend of 2 cents and special dividend of 3 cents.
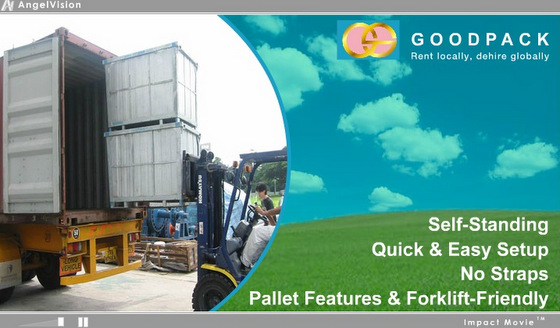